1
/
of
1
PARARAJA77
Mainkan Slot Favorit Anda di PARARAJA77: Kemenangan Besar Menanti
Mainkan Slot Favorit Anda di PARARAJA77: Kemenangan Besar Menanti
Regular price
Rp 0,00 IDR
Regular price
Sale price
Rp 0,00 IDR
Unit price
/
per
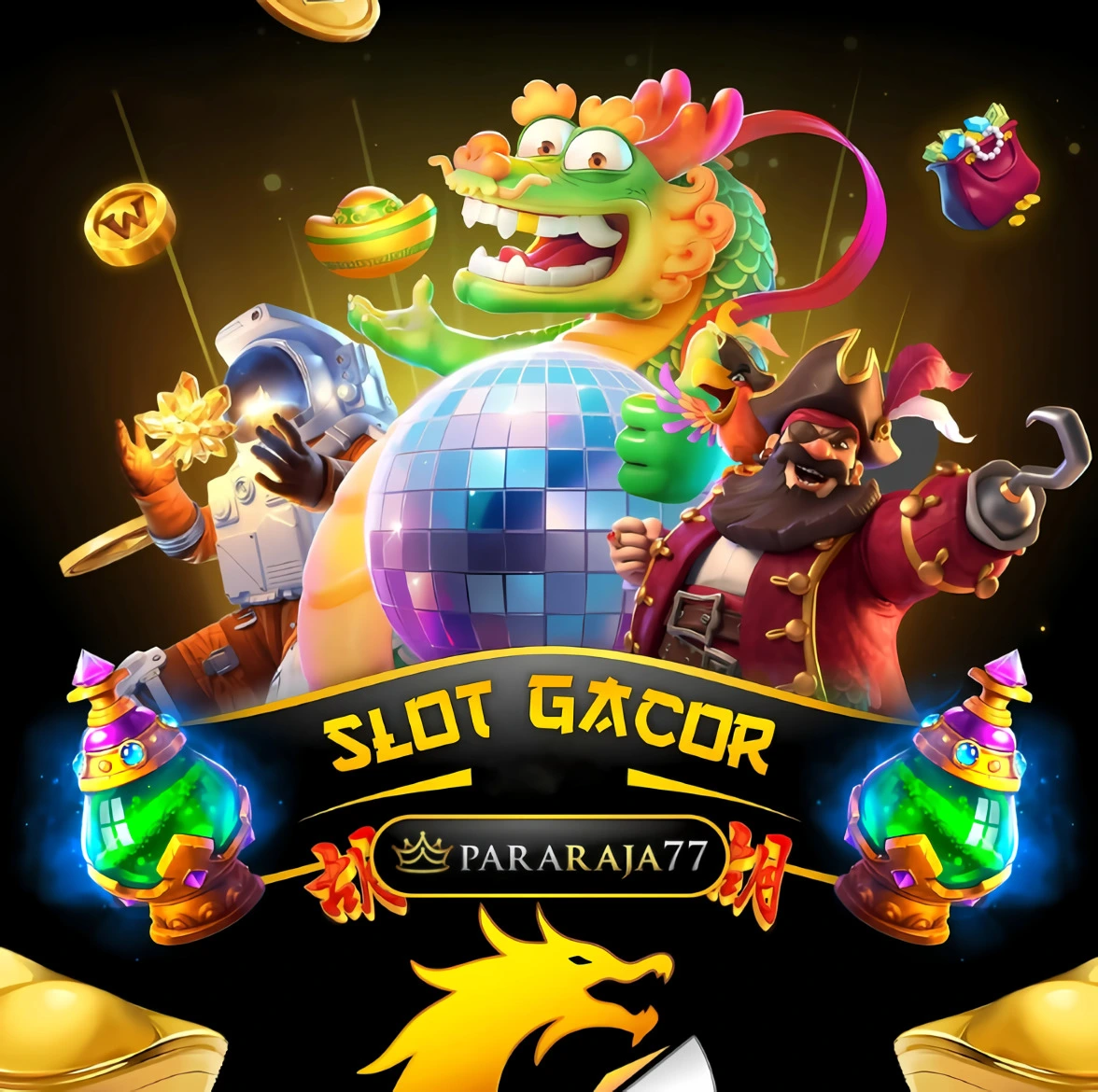
Subscribe to our emails
Join our email list for exclusive offers and the latest news.
- Choosing a selection results in a full page refresh.
- Opens in a new window.